TECHNICAL PAPER #4
UNDERSTANDING BIOGAS GENERATION
By
Richard Mattocks
Technical Reviewers
J.B. Farrell
C. Gene Haugh
Daniel Ingold
Published By
VITA
1600 Wilson Boulevard, Suite 500
Arlington, Virgnia 22209 USA
Tel: 703/276-1800 . Fax: 703/243-1865
Internet: pr-info@vita.org
Understanding Biogas Generation
ISBN: 0-86619-204-2
[C]1984, Volunteers in Technical Assistance
PREFACE
This paper is one of a series published by Volunteers in
Technical
Assistance to provide an introduction to specific
state-of-the-art
technologies of interest to people in developing countries.
The papers are intended to be used as guidelines to help
people choose technologies that are suitable to their
situations.
They are not intended to provide construction or
implementation
details. People are
urged to contact VITA or a similar organization
for further information and technical assistance if they
find that a particular technology seems to meet their needs.
The papers in the series were written, reviewed, and
illustrated
almost entirely by VITA Volunteer technical experts on a
purely
voluntary basis.
Some 500 volunteers were involved in the production
of the first 100 titles issued, contributing approximately
5,000 hours of their time.
VITA staff included Leslie Gottschalk
as primary editor, Julie Berman handling typesetting and
layout,
and Margaret Crouch as project manager.
Richard Mattocks, author of this paper, is an environmental
scientist with Draper-Aden Associates, Inc.
He specializes in the
management of solid waste materials and the recovery of
biomass
products, and is currently researching various uses of biogas
digester effluent, particularly its use as an animal feed
source.
Reviewers J.B. Farrell, C. Gene Haugh, and Daniel Ingold are
also
specialists in the area.
Farrell is a chemical engineer by training
and chief of the Sludge Management Section of the U.S.
Environmental
Protection Agency's Municipal Environmental Research
Laboratory. Haugh
heads the Department of Agricultural Engineering
at Virginia Polytechnic Institute.
Ingold, a biophysicist, is
a research engineer at Appropriate Technology Corporation.
VITA is a private, nonprofit organization that supports
people
working on technical problems in developing countries.
VITA offers
information and assistance aimed at helping individuals and
groups to select and implement technologies appropriate to
their
situations. VITA
maintains an international Inquiry Service, a
specialized documentation center, and a computerized roster
of
volunteer technical consultants; manages long-term field
projects;
and publishes a variety of technical manuals and papers.
UNDERSTANDING BIOGAS GENERATION
by VITA
Volunteer Richard Mattocks
I. INTRODUCTION
HISTORY
Biogas is a by-product of the biological breakdown--under
oxygen-free
conditions--of organic wastes such as plants, crop residues,
wood and bark residues, and human and animal manure.
Interest in
biogas as a viable energy resource has spread throughout the
globe in the past two decades.
Biogas generators or digesters
operate throughout Asia, for example, with more than 100,000
reported in India, about 30,000 in Korea, and several
million in
China. Many more are
operating in the Middle East, Africa,
Oceania, Europe, and the Americas.
Biogas is known by many names--swamp gas, marsh gas,
"will o' the
wisp," gobar gas.
It contains about 50 to 60 percent methane, the
primary constituent of natural gas.
Biogas is produced naturally
from the degradation of plants in such situations as rice
paddies, ponds, or marshes.
Because it can also be produced and
collected under controlled conditions in an airtight
container,
it can be an important energy source.
Ancient Chinese experimented with burning the gas given off
when
vegetables and manures were left to rot in a closed
vessel. More
recently, Volto, Beachans, and Pasteur worked with
biogas-producing
organisms. At the
turn of the 20th century, communities in
England and Bombay, India, disposed of wastes in closed
containers
and collected the resulting gas for cooking and lighting.
Germany, the United States, Australia, Algeria, France, and
other
nations constructed such methane digesters to supplement
dwindling energy supplies during the two world wars.
NEEDS SERVED BY THE TECHNOLOGY
Biogas generators or digesters yield two products: the
biogas
itself, and a semi-solid by-product called effluent or
sludge.
Biogas systems are most popular for their ability to produce
fuel
from products that might otherwise be wasted--crop residues,
manures, etc. The
fuel is a flammable gas suitable for cooking,
lighting, and fueling combustion engines.
The digested waste--sludge--is a high quality
fertilizer. The
digestion process converts the nitrogen in the organic
materials
to ammonium, a form that becomes more stable when plowed
into the
soil. Ammonium is
readily "fixed" (bonded) in soil so that it can
be absorbed by plants.
In contrast, raw manure has its nitrogen
oxidized into nitrates and nitrites, which do not
"fix" well in
soil and are readily washed away.
Moreover, biogas systems offer a means to sanitize
wastes. Simply
put, these systems are capable of destroying most bacteria
and
parasitic eggs in human and animal wastes, enabling the
digested
sludge to be applied safely to crops.
Tests have shown that
biogas systems can kill as much as 90 to 100 percent of
hookworm
eggs, 35 to 90 percent of ascarid (i.e., roundworms and
pinworms),
and 90 to 100 percent of blood flukes (i.e., schistosome
flukes, which are found in water snails that commonly live
in
paddy fields and ponds).
Biogas systems are also capable of digesting municipal
sewage,
which is a major source of pollution.
Using biogas systems in
this way substantially reduces the potential for
environmental
pollution.
Finally, agricultural and animal wastes, the major raw
materials
for biogas production, are usually plentiful in rural areas.
People living in rural communities, who are often subjected
to
the price and supply fluctuations of conventional fuels and
fertilizers, can benefit directly from biogas systems.
It should be noted that, while this paper focuses on the
production
of biogas for fuel, in some applications the gas is
considered
to be the by-product of the process.
Some digesters in
China, for example, are used primarily for treating sewage
and
producing fertilizer, and only secondarily for producing
fuel.
II. OPERATING
PRINCIPLES
BASIS OF THE TECHNOLOGY
Biogas generation is a process that takes place in an
oxygen-free
environment. It uses
anaerobic bacteria--bacteria that live only
in the absence of oxygen--to break down complex organic
compounds
in fairly well-defined stages.
The process is called anaerobic
digestion. It
produces biogas, a gas composed of approximately 50
to 60 percent methane, 40 to 50 percent carbon dioxide, as
well
as water vapor and a small quantity of nitrogen, sulfur, and
other trace compounds.
Biogas is flammable, which is what makes
it useful, but it has a relatively low heat content,
approximately
6.1 Calories per liter (around 600 BTU per cubic foot).
Compare
this with pure methane, which has a heat value of 995 BTU
per cubic foot, or natural gas with over 1,000.
Nevertheless,
biogas can be an important fuel source for many
applications.
A biogas digester is the device in which the digestion
process
occurs. The organic
feedstock, which is called the substrate, may
consist of night soil, manure, crop or kitchen residues, or
similar materials.
The substrate is usually diluted with water,
and is thoroughly mixed into a slurry; crop residues and
vegetation
are usually cut or chopped into small, fairly uniform
pieces. It is then
fed into the digester and permitted to undergo
degradation in a sealed oxygen-free chamber.
When digestion is
completed, the material is discharged, or removed from the
digester.
The biogas is collected for direct usage or pressurized for
subsequent use. The
discharged material is called effluent, or
sludge.
The actual breakdown of organic material inside the digester
is a
three-stage process that leads to the production of methane
(Figure 1).
ubg1x3.gif (600x600)
In the first stage, numerous organisms release enzymes that
attack specific bonds in complex protein, carbohydrate, and
lipid
compounds in the incoming substrate.
This stage of degradation
converts the compounds into simpler molecules.
Another set of
organisms further degrades the molecules to form short-chain
volatile fatty acids.
At this point, various methane-producing
organisms (or methanogens) use carbon dioxide or volatile
fatty
acids to produce biogas (a mixture of methane and carbon
dioxide).
The principles of anaerobic digestion are the same
regardless of
the digestion vessel.
Organic material is loaded into a fairly
warm, temperature-controlled, oxygen-free environment and
methane
is produced after acclimatization.
The makeup or quality of
incoming material to be digested, the vessel, and the
surrounding
environment influence the digester efficiencies.
The production
of gases is greater when the digester is operated at a
relatively
high temperature, when the substrate is stirred or otherwise
agitated, and when system conditions are kept fairly
constant. A
more detailed discussion of these and other factors
influencing
digester efficiency follows.
In general, however, the important
objective to keep in mind when operating a biogas digester
is the
production of the greatest volume of biogas in the shortest
possible time.
FACTORS INFLUENCING PERFORMANCE AND SIZE OF BIOGAS DIGESTERS
Researchers are only now gaining a better understanding of
the
metabolic process in biogas digesters.
They do know, however,
that methane-producing organisms (called methanogens)
"prefer" to
channel energy, or calories (derived by breaking down
incoming
substrate), to methane rather than use the energy to
construct or
satisfy internal cellular needs.
As such, methanogens do not
adapt well to changes in their environment that may require
them
to increase their numbers or adjust their internal
mechanisms. If
the environmental changes are significant enough, the
methanogens
may slow or even stop their work.
Changes that may affect the behavior of the bacteria and
thus the
performance of the digester include variations in the
substrate,
presence of certain toxic chemicals, gas pressure,
temperature,
and the amount of time the material remains in the digester.
Other factors that could have a major impact on the
operating
performance of a biogas digester include biological balance/
acidity, solids concentration, agitation, feedstock,
pretreatment,
and the carbon-to-nitrogen ratio.
The primary factors that could affect the size of a biogas
digester
include the type and amount of feedstock, the rate at which
it is loaded, and hydraulic retention time.
Factors Influencing Digester Operating Performance
Biological Balance/Acidity
Methanogens--methane-producing organisms--live in a
syntrophic,
or complementary, relationship with certain other
microorganisms
that consume the feedstock and produce simple acids as part
of
their metabolism.
The simplest acids are essential to the metabolic
processes of the methanogens.
As acid-producing organisms
tend to choke in their own acetic by-products, methanogens
cooperate
by consuming these by-products in the methane-producing
process.
Given sufficient time to establish the proper ratio of
methane-producing
organisms to acid-producing organisms, a homeostasis,
or stability, will occur with a pH of about seven in a
digester.
A digester fed poultry or high nitrogen waste may stabilize
at a
pH of eight or greater.
The objective here is to create a stable working
relationship
among the microbial population in the digester.
This implies the
need for fairly constant operating temperatures and
feedstock
characteristics.
Conversely, any rapid variations of these conditions
will cause the microbial population to shift dramatically
and possibly upset the overall system balance in the
digester.
For example, if the methane-producing organisms become
dormant
due to, say, temperature fluctuations, the pH will drop so
low
as to incapacitate them.
Maintaining a stable pH requires stabilizing the feedstock
as
well as the operating temperature in the digester.
If this proves
impractical, adding lime or other buffering compounds to the
digester will prevent the pH from falling.
Note that the correct
amount and type of buffering compound can be determined only
on a
case-by-case basis.
Four additional factors that could affect the overall system
balance in the digester are:
1. The concentration
of the incoming solid waste could vary and
either increase
or decrease the amount of food to be consumed
by the digester.
2. Removing the
slurry (the mixture of water and substrate
added to the
digester) from the digester or replacing it
altogether, each
day, will change the average age of the
organisms in the
digester.
3. The average
characteristics of the material being consumed
by the microbial
population in the digester will change in
response to any
fluctuations in the amount of feedstock
material removed
each day.
4. The temperature,
as well as the contents of the water used
to dilute the incoming
waste, will alter the nature of the
food to be
consumed by the digester.
Operating Temperature
Operating temperature is another factor influencing digester
efficiency. A
digester can operate in three temperature ranges:
(1) the low temperature, psycrophilic bacteria range, which
is
less than 35[degrees]C (90[degrees]F); (2) the medium
temperature, mesophilic
bacteria range, which is 29 to 40[degrees]C (85 to
105[degrees]F); and (3) the
high temperature, thermophilic bacteria range, which is 50
to
55[degrees]C (135 to 140[degrees]F).
Organic material degrades more rapidly at
higher temperatures because the full range of bacteria are
at
work. Thus, a
digester operating at a higher temperature can be
expected to produce greater quantities of biogas.
The disadvantage
of an elevated-temperature digester is that even minor
changes in system conditions could offset digester
efficiency or
productivity.
Moreover, an additional source of energy will likely
be required to maintain the digester contents at a constant
higher temperature.
Though operating temperature is critical, stabilizing the
temperature
and keeping it stabilized are even more important.
Variations
of plus or minus 1[degree]C in a day may force the
methane-producing
organisms into periods of dormancy.
These organisms
consume acids, and without them acids will accumulate and
the pH
will fall, impeding the effectiveness of the whole biogas
system.
In northern latitudes or colder climates, the volume of
methane
will be substantially less unless specific provisions are
made to
preheat the incoming substrate and maintain the digester
temperature.
Thus, in colder climates, larger digesters will likely be
required. Moreover,
the amount of digester surface constructed
above ground should be reduced when temperatures are low.
One way to overcome the problem of lower temperatures is to
dilute the daily incoming waste material with preheated
(solar-heated)
water. Or you can
construct a greenhouse or compost pile
around the digester.
Note that the amount and type of waste to be degraded as
well as
the operating temperature are two important factors
governing
digester size.
Solids Concentration
The moisture content of the digestion liquor (waste that is
diluted) should be in the range of 5 to 12 percent total
solids.
The percentage of total solids should include a minimum of
inorganic
sands and soils.
Incoming waste products may have to be
diluted to a consistency of slightly thick cream.
A rule of thumb
for diluting cattle waste is 2.5 parts water for every one
part
of relatively dry waste or one part water for every one part
of
fresh manure.
Stirring the Digester Contents
The microorganisms degrading the waste material are living,
metabolizing
creatures that produce their own metabolic by-products.
To prevent the bacteria from stagnating in their own waste
products,
and thus to promote a more rapid digestion, stir or agitate
the digester contents by paddle, Scraper, piston, or in more
sophisticated settings, by gas recirculation.
Agitation also helps to minimize the build-up of internal
fibrous
scum on top of the digestion liquor.
Failure to break the scum
may result in excessive gas pressures forcing substrate out
of
the openings instead of permitting the gas to escape through
gas
transport lines. The
scum may also plug the digester.
Digesters
that are fed higher volumes of fibrous waste may require
special
design considerations.
Feedstock Pretreatment
Feedstocks sometimes require pretreatment to increase the
methane
yield in the anaerobic digestion process.
Pretreating the feedstock
(with alkaline or acid treatments, for example) breaks down
the complex organic structures into simpler molecules that
are
then more susceptible to microbial degradation.
Thus, you may want to pretreat any incoming substrate whose
volatile solids are not readily degradable.
Note that microorganisms
do not readily act upon rice hulls or sawdust.
Fibrous wastes also require special handling.
Wastes with long
fibers such as straw should be chopped or broken.
Any given waste
will digest more rapidly, and possibly even more completely,
when
broken into bits.
Thus, the finer the waste is shredded, ground,
or pulped, the easier the digestion process will be.
Scientific research has determined that minimum levels of
nickel,
cobalt, and iron are required for methanogens to degrade
organic
wastes more efficiently.
This is of little immediate consequence
to most farmers, as chemical analysis is required to
determine
whether addition of these elements would be helpful.
Carbon-to-Nitrogen Ratio
If the carbon-to-nitrogen ratio is either too high or too
low, or
fluctuates substantially, the digestion process will slow or
even
stop. To act
efficiently on the substrate, microorganisms need a
20-30:1 ratio of carbon to nitrogen, with the largest
percentage
of the carbon being readily degradable.
Digesters have efficiently
operated on poultry waste with a 5-7:1 ratio.
The key
here is to keep the quantity as well as the characteristics
of
the incoming substrate constant.
One note of caution: some carbon compounds resist being
broken
down. Lignin, for
example, which all land plants use to help
stiffen and support themselves, is the least readily
degradable
carbon compound. The
amount of lignin increases proportionally
with plant age.
Thus, old grass contains more lignin than new
grass, and wood contains more of it than do leaves.
Remember, any
substrate that contains a high percentage of lignin will not
readily decompose in the biogas digester as well or as
completely
as substrates that contain lesser amounts.
Thus, horse dung and
mature vegetative waste material are probably not good
feedstocks,
because they contain a high fraction of non-degradable
lignin.
Presence of Certain Toxins
Certain medications (e.g., antibiotics used in animal feeds
or
injected into animals), feed additives, pesticides, and
herbicides
may have adverse effects on anaerobic bacteria, particularly
the methanogens. For
example, lincomycin (frequently used in
treating swine) and monensin (often used in treating cattle)
are
two antibiotics that will harm these bacteria and
immediately
halt methane production.
Factors Influencing Digester Size
Digester design depends basically upon the availability and
type
of waste to be fed to the digester, as well as the amount of
gas
and/or fertilizer required.
Large digesters are generally designed
after establishing system operating conditions through
laboratory analysis.
Small digestion plants are generally designed
based on past experiences with a particular substrate.
A distinct advantage of small digesters over large ones is
that
their contents require less vigorous and less frequent
stirring
(only several times a day) to prevent scum buildup and thus
increase the production of biogas.
A principal disadvantage of
these digesters, on the other hand, is that their operating
temperatures tend to fluctuate more often and to a much
greater
degree.
Nevertheless, feeding a biogas digester--regardless of its
size--any
number of individual or combined feedstocks or organic
materials
will result in the production of biogas as long as the
proper conditions exist and are kept fairly stable.
These conditions
were researched initially for sewage treatment plants and
more recently are the subject of intense investigation
toward
meeting the waste management needs of various agricultural
and
specialized industries.
Type and Availability of Raw Waste Material
Husbandry practices can influence the quantities of manure
available
for use in the digester.
For example, cattle in pasture will
scatter their waste over a large grazing area, making waste
collection difficult.
Conversely, a herd that spends most of the
day in a confined area (e.g., a corral) will deposit waste
in a
concentrated area, making it possible to collect waste more
easily. Moreover,
manure deposited directly in the field will
likely contain a lot of soil or grit, which will eventually
clog
the digester, and thus not be suitable for the production of
biogas.
The amount of manure produced per animal per day
varies. For
example, one may expect about six pounds per day from a
1,000
pound beef or dairy cattle and about nine or 10 pounds per
day
from 1,000 pounds of broiler chicken.
Remember, increased gas
production is directly proportional to the amount of
volatile
solids in the raw waste used.
Under optimum collection conditions (i.e., when animal is
confined),
you get:
4 lb of manure per 100-lb sheep
80 lb of manure per 1,000-lb dairy cattle
60 lb of manure per 1,000-lb beef cattle
10 lb of manure per 200-lb pig
45 lb of manure per 1,000-lb horse
0.2 lb of manure per 4-lb poultry layer
The rule of thumb here is that the waste material from two
adult
cattle will usually supply the gas required for cooking food
for
a family of four.
Comparable quantities of other waste may produce
slightly more or slightly less gas.
If you are considering relying on the use of a significant
amount
of vegetable waste in your digester, you need to know when
such
material will be available in the greatest quantities.
For example,
water hyacinth may be available year round in some climates,
while grain straw or other crop residues will be most
plentiful
only at harvest.
Wilted or semi-dried vegetation may require the addition of
water
in order to maintain optimum solids concentration.
Freshly-cut
young vegetation may require less dilution than freshly cut
older
plant material.
Organic Loading Rate
The organic loading rate refers to the number obtained when
the
weight of the volatile solids loaded each day into the
digester
is divided by the volume of the digester.
("Volatile solids"
refers to the portion of organic material solids that can be
digested. The
remainder of the solids are fixed. The
fixed solids
and a portion of the volatile solids are
non-degradable. Organic
material may also contain a substantial amount of water.)
Loading rate is an important parameter, since it tells us
the
amount of volatile solids to be fed into the digester each
day.
At high loading rates, the feeding has to be more nearly
continuous
(perhaps hourly). At
lower loading rates, the biogas
digester needs to be fed only once a day.
Digesters are designed to receive and treat from 0.1 to 0.4
pounds of volatile solids per cubic foot of digester volume.
Although the actual loading rate depends on the type of
wastes
fed to the digester, 0.2 pounds of volatile solids per cubic
foot
of digester volume (approximately 3 kg per cubic meter) is a
frequently used design parameter.
This means a digester used to
process mainly manure should be designed to accommodate from
20
to 120 cubic feet of digester volume per 1,000 pounds of
live
animal. (The actual
amount varies from species to species.)
Here, it is important to remember that a digester must be designed
on the basis of the amount of waste that can be collected
and actually fed to the digester, not on the quantity of
waste
produced.
For illustration, the following estimates are useful:
1 lb of volatile solids per 200-lb pig per day
1 lb of volatile solids per 1-lb sheep per day
0.04 lb of volatile solids per 4-lb poultry layer per day
6 lb of volatile solids per 1,000-lb beef or dairy cattle
per day
9 to 10 lb volatile solids per 1,000 pounds of poultry layer
The percentage of water in animal waste on a unit volume
basis is
around 75 to 95 percent.
Of the solids in the waste, about 70
percent are volatile.
Percentage of water in vegetable and plant
wastes varies from 40 to 95 percent.
Of that, the percentage of
volatile solids varies from 50 to 95 percent.
The amount of
biogas produced from vegetable and plant waste varies
because
various crops have differing biomass production rates.
With time, constant temperature, and a uniform incoming
substrate,
a digester will stabilize.
The rules of thumb for any
digester include:
1. Incoming
substrate 5 to 12 percent total solids;
2. 0.2 to 0.5 pounds
volatile acids per cubic foot of digester
volume;
3. 1 to 2 pounds raw
manure per cubic foot of digester space
per day; and
4. 0.2 to 1.0 unit
volume of biogas produced per unit volume of
digester.
The actual amount of biogas that will be produced can be
determined
by experimentation under conditions similar to those at the
site. One should
experiment with various types of waste, the
amount of water used to dilute an incoming waste, operating
temperature, and feeding (loading) frequency.
A source of potential confusion in determining digester size
is
the means to measure gas production.
When reading literature on
biogas digesters, make sure that the gas production under
discussion
is in comparable units.
Gas produced in a digester is biogas,
of which 50 to 60 percent is methane; the remainder is
carbon dioxide and other gases.
Biogas volumes are distinct from
methane volumes.
Other ways of quantifying gas include: gas
volumes per volume of digester, gas volumes per 1,000 pounds
of
live weight of an animal species, gas volumes per pound of
volatile
solids added, and gas volumes per pound of volatile solids
destroyed.
Hydraulic Retention Time
Hydraulic retention time (HRT) is the average number of days
a
unit volume of substrate is to remain in the digester.
Put another
way, HRT is the volume of material already in the digester
divided by the average amount of incoming daily feedstock,
or the
average age of the digester contents.
The HRT will vary from 10
to 60 days, and is an important parameter because it
influences
the efficiency of the biogas digester.
Closely controlled digesters will average about 20 to 25
days
retention time.
Shorter retention times will create the risk of
washout, a condition where active biogas bacteria are washed
out
of the digester at too young an age, making the population
of
bacteria unstable and potentially inactive.
Daily conversion of
organic material to methane will continue to increase per
unit
increase of weight (i.e., age) of bacteria up to a certain
point.
Thereafter, methane production will drop off per unit weight
(or
age) of bacteria.
Note that a longer retention time requires a larger digester
and
more capital for its construction.
Recall, however, that the
smaller the digestion vessel, the less time the
methane-producing
bacteria will have to act on the available substrate and
thus the
more likely the biogas system could malfunction.
One should
consider all these factors carefully before choosing a
system.
III. DESIGN
VARIATIONS
There are two general design characteristics of digesters:
batch
feed and continuous feed.
The batch digester is loaded, sealed,
and after a period of gas collection, emptied.
A batch digester
can essentially be any suitably sized container or tank that
can
be sealed and fitted with a means to collect the
biogas. The
continuous feed digester receives substrate on a continuous
or
daily basis with a roughly equivalent amount of effluent
removed.
There are many possible design variations for continuous
feed
digesters.
CONTINUOUS FEED DIGESTERS
The design variations for continuous feed digesters can be
divided
into four distinct types: the Indian design, the Chinese
design, the sewage treatment plant, and the hybrid
design. Each
of these types, along with cost and construction
considerations,
is described in the sections that follow.
Indian Design
The Indian, or Khadi, design (Figure 2) is based on the
principle
ubg2x12.gif (600x600)
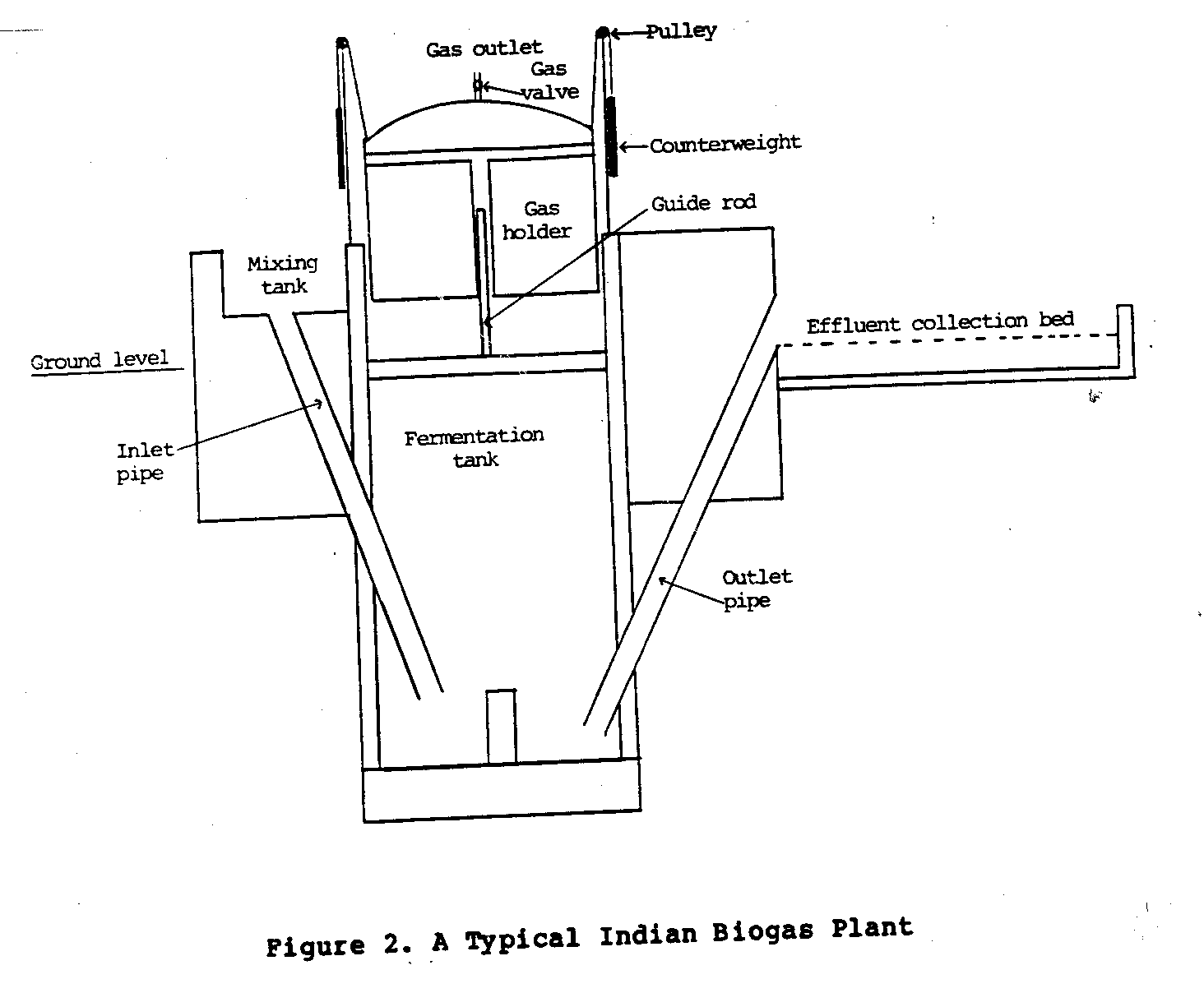
that gas produced will lift a bell-shaped dome located above
the
digestion vat.
Substrate enters one side of the digester and
displaces effluent out the other side.
As gas is produced, it is
collected under the dome, forcing it to rise.
The dome descends
as gas is forced out of the digester into the gas transport
lines.
Chinese Design
The gas storage chamber in the Chinese design
characteristically
has a fixed top (Figure 3).
Substrate enters one side; effluent
ubg3x13.gif (600x600)
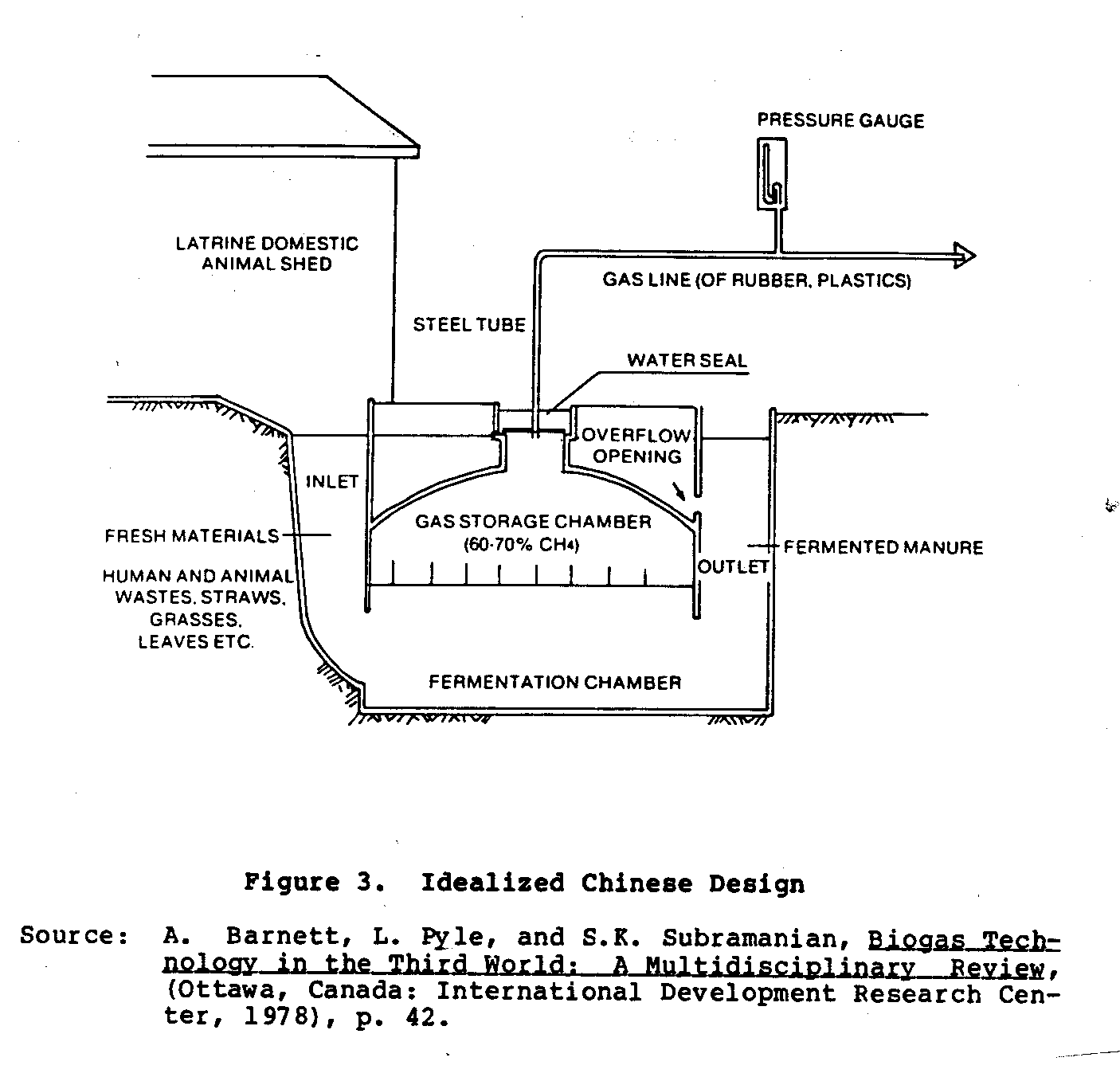
exits the other side.
Gas produced accumulates under the dome and
above the vessel contents.
Increases in gas volume displace
digester contents into the displacement, or overflow,
chamber.
The materials forced into the displacement chamber will, by
virtue of gravity, attempt to flow back into the
digester. The
attempt by the displaced liquor to flow back into the
digestion
vessel creates the pressure to force the gas into the gas
transport
line. As the gas is
used, materials displaced into the
displacement chamber will flow back into the vessel.
Sewage Treatment Plant
Though the designs associated with treating sewage or
industrial
wastes follow the same basic principles of the Indian and
Chinese
designs, they are much more complex and more efficient.
The
digester content is stirred either by paddle or gas
recirculation.
Temperature controls are much more stringent and digester
content may be heated.
The effluent exits the plant and is thickened
prior to final disposal.
Gas is tapped from the digester,
possibly pressurized, and used for heating purposes or
flared; it
may be used for process heat in the digester.
The sewage treatment
plant principles may be employed on a much smaller scale
with lower levels of technology.
Figure 4 shows a high-technology
ubg4x14.gif (600x600)
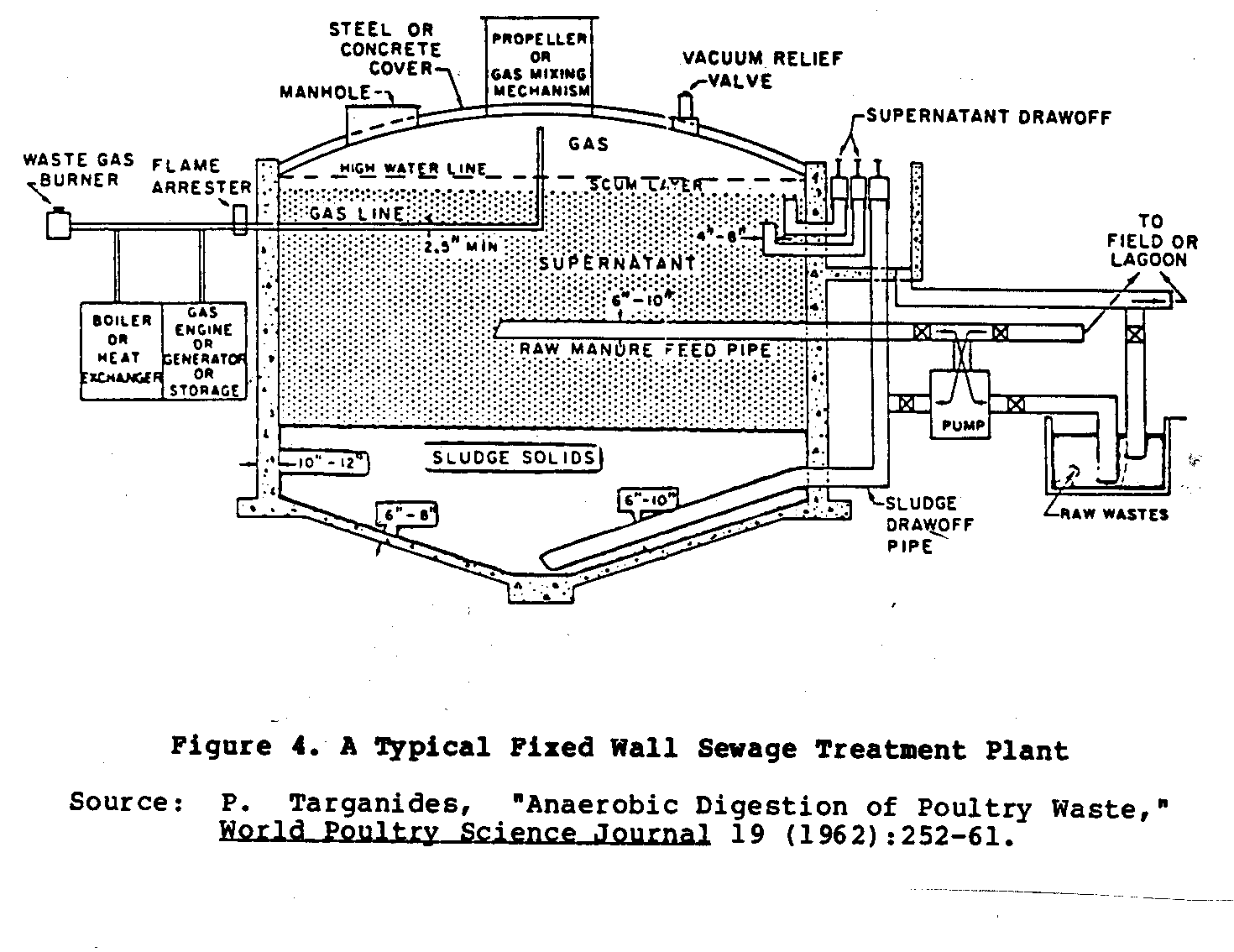
sewage treatment plant.
Hybrid Designs
Hybrid digesters imitate the principles employed in other
designs,
except that digestion vessels conform to the least
expensive,
most readily available construction materials.
They can be
built from available scrap materials, plastic bags, or
covered
troughs. A very
simple design is the end-to-end welding of 55-
gallon oil drums to create a long, narrow, small-volume
continuous
feed digester. With
hybrid digesters, care must be taken
not to let construction economy offset digester efficiency
or
productivity. Figure
5 shows a low-technology hybrid digester.
ubg5x16.gif (600x600)
Comparison of Continuous Feed Digesters
The more sophisticated biogas digesters require skilled
people to
build, operate, and maintain them.
Such digesters will likely be
more economically feasible if they are used to process large
quantities of waste.
Although a high-technology digester does
produce considerably more gas than either the Indian or the
Chinese design, it has higher capital and operating costs
and
requires careful monitoring on a daily basis.
The Indian and Chinese designs are less expensive and easier
to
build and operate, but those benefits are countered by
fairly
inefficient gas production.
Moreover, leakage may become a problem
if the digesters are not maintained well.
Although the Indian
design produces slightly more gas than the Chinese design,
it is
slightly more expensive and has the added maintenance
requirements
associated with the floating dome.
APPLICATIONS
Biogas can be burned directly as a fuel for cooking,
lighting,
heating, water pumping, or grain milling, and can also be
used to
fuel combustion engines.
In larger applications where scale and
skills warrant, biogas can be pressurized and stored,
cleansed
for sale to commercial gas suppliers, or converted to
electricity
and sold to power grids, to meet peak energy needs.
Gas transport lines are connected to the gas-collection
chamber
of the digester (the floating dome of the Indian style
digester).
The gas has a high moisture content.
It is necessary to devise a
way to remove the moisture before the gas is used.
One way is to
slope the transport line back toward the digester so that
the
moisture will flow down the line back into the tank.
If this is
not practical, it will be necessary to install a sump, or
chamber,
in the gas line to collect the moisture.
Biogas is also very corrosive.
It may contain dangerous amounts
of hydrogen sulfide, a poisonous flammable gas that produces
a
highly corrosive acid when mixed with water.
For this reason, gas
transport lines must be corrosion resistant.
Polyvinyl chloride
(PVC) plastic pipe is a good choice for gas lines because it
is
durable, corrosion resistant, and usually economical.
Because the
gas is so corrosive, it may have to be cleansed before it is
used, particularly in engines.
While biogas is an excellent fuel, it does have a fairly low
energy value for its volume--500-600 BTUs per cubic
foot--and the
pressure in the distribution lines may be low.
Lamps, stoves, refrigerators,
and other appliances require specially designed jets
to offset the low energy value and the low gas
pressure. To
stabilize the flame on a cookstove, for example, the jet
forcefully
shoots the biogas up through and out of the burner.
Jets
can either be purchased or built easily from locally
available
materials.
The amount of methane required daily per household will
vary.
About 0.5 to 1.0 cubic meter of biogas is required per
family
member for food preparation alone, and roughly one cubic
meter of
biogas is produced per 1,000 pounds of animal.
Meeting one family
member's cooking requirements, then, requires two or three
healthy dairy or beef cows, or eight to 10 pigs (weighing
150 to
250 pounds each), or over 500 chickens.
The amount of waste
material produced by these animals varies with their health
and
diet and will influence the number of animals required.
Collecting
more than 30 to 40 pounds of waste daily per 1,000 pounds of
live weight per animal will increase the amount of gas
produced
per animal.
The effluent leaving the digester at the end of the
digestion
period is spread on farmland much as the undigested manure,
etc.,
is used. Research
has been performed on using the digester effluent
to feed cattle or to promote algal growth in fish ponds,
as is done in some Chinese aquaculture installations.
CONSTRUCTION MATERIALS
The equipment and materials required for digester
construction
depend upon the level of technology employed.
The basic Chinese
design requires cement, sand, clay, lime, and bricks.
Sulfate-resistant
cement should be used if available due to the corrosive
nature of the gas and slurry.
The Indian design requires these
same materials, plus some welding and iron works.
The higher
technology designs may require some specific machinery and
electronics.
The following are generalized examples of the types and
quantities
of materials required to build similar sized Chinese- or
Indian-style digesters.
A Brace Research Institute publication (1976) reports the
following
materials for an Indian-style, 3-cubic meter digester that
should produce sufficient gas for the cooking needs of a
family
of six to eight members:
*
9 meters galvanized iron sheet
*
3,200 small construction bricks
*
25 50-kg bags of cement
*
12 cubic meters of sand
*
various angle irons, iron pipes, etc.
The Khadhi and Village Industries Commission in Bombay,
India,
lists (in part) the following materials for a 3-cubic meter
horizontal digester:
*
2,870 bricks
*
3.2 cubic meters of sand
*
1.9 cubic meters of 1/2" to 3/4"
rock
*
24 bags of cement
*
7.5 meters of sheet steel
*
various angle irons, pipes, reinforcing
rods.
A masonry wall Chinese style digester of 8 cubic meters
calls for:
*
400 kg of cement
*
1,000 kg of sand
*
1,000 bricks
*
various plastic tubes for gas delivery.
Small-scale, nonpermanent digesters can be constructed of
oil
drums or uniformly-supported plastic bags.
The above materials are meant only for demonstration
purposes.
Actual type and quantity of materials required depend on
design.
Note, however, that smaller biogas digesters are generally
built
with readily available materials.
SKILLS REQUIRED TO PRODUCE AND OPERATE A BIOGAS DIGESTER
The basics of a digester can be creatively adapted by
competent,
local craftspeople working with locally available materials.
The Chinese design requires the skills of a competent
mason. The
Indian design requires the skills of a competent mason as
well as
an iron worker and welder.
More sophisticated digesters for larger scale applications
require
plumbers and electricians.
Careful planning is required
prior to building such facilities.
Once constructed, the digester requires the daily attention
of a
semiskilled individual.
Each day, the digester must be fed and
agitated, and the effluent properly disposed of. Just as a
caretaker
tends to a herd of animals, the individual responsible for
the digester must understand the operational procedures.
This
person must maintain not only the digester's physical plant,
but
also ensure that the gas transport line and gas utilization
system
are operative and in good repair.
COSTS
Costs for construction are governed by the level of
technology
employed. They range from a few dollars for digesters built
of
readily available scrap to a few hundred dollars for a small
family, Chinese-style digester, and from several hundreds of
dollars for a small-scale Indian-style digester to several
hundreds
of thousands of dollars for a large-scale operation.
A rule
of thumb for comparable sized digesters is that the
Chinese-style
digester costs half that of a "drum"-style Indian
digester. A
more sophisticated digester will cost at least three times
that
of an Indian-style digester of comparable volume.
Actual costs depend upon the availability of resources.
Large
numbers of semi-skilled laborers, for example, suggest that
construction
of a Chinese-style digester would be more economical.
On the other hand, even though an Indian-style digester
costs
more initially to construct, it is nevertheless more
efficient,
requires less maintenance, and produces more gas than a
Chinese-style
digester. Larger,
more sophisticated digesters require
markedly higher initial capital costs than smaller, less
complex
units. However, they
are more efficient in terms of the total
volume of organic material that can be handled per unit
volume of
digester, and they produce more gas per unit of organic
material
handled. To do a
thorough cost analysis one must take into
account such factors as inflation, interest rates, operating
costs, maintenance expenses, labor costs, and the value of
replacing
conventional fuels (e.g., oil, gas) with biogas.
EFFICIENCY
The amount of biogas varies from 30 to nearly 100 cubic feet
per
1,000 pounds of live body weight.
Thus, there is no universal
formula to determine biogas efficiency.
To do so, one must consider
many factors.
For example, biogas efficiency varies, depending upon how
the
biogas is used.
Biogas plants use organic wastes, which, if not
fed to a digester, are at best spread over land or at worst
directly burned.
Although direct combustion of dung or grasses
yields at best 10 percent of the available energy, the
nutrient
values of such wastes are severely reduced.
Biogas systems yield
40 to 50 percent, or better, of the thermal potential of
organic
wastes and yield a fertilizer of superior quality.
Composting
provides excellent fertilizer with no gas.
Other, much more
sophisticated procedures are also available for more
efficient
removal of energy from waste.
Moreover, efficiency varies with the type of digester, the
operating
conditions, and the type of material loaded into the
digester.
All else equal, the Chinese-style digester produces about
half as much gas as the Indian-style digester, which in turn
yields less than half the gas of more sophisticated
units. The
Chinese design, the Indian design, and the high-technology
designs,
respectively, yield about 0.2 to 0.3, 0.5 to 0.7, and 1.0
to 2.0 volumes of biogas per volume of digester.
And, in general,
digesters produce more gas with poultry waste (about 100 or
so
cubic feet of biogas per 1,000 pounds of live poultry
weight)
than they do with cattle waste (25 to 30 cubic feet per
1,000
pounds of live cattle weight).
Apart from these factors, the key to maintaining efficiency
is to
feed the digester a uniform feedstock daily, to maintain a
constant
operating temperature, and to agitate the contents
regularly.
MAINTENANCE REQUIREMENTS
Biogas digesters require careful maintenance.
Operators should be
responsible for the following maintenance activities:
*
Daily Activities: Collect and prepare the
feedstock, and
load it into
the digester. Collect the liquid
effluent
from the
digester. It may be spread over fields,
used to
fertilize
fish ponds, or dried for later use.
*
Periodic (at regular intervals) Activities:
Remove the
digester
contents, including any solids that have accumulated
at the bottom
of the digester. Because of the
potentially
corrosive nature of the digester contents
(slurry as
well as gas), check all metal components of
the digester
to see whether they need to be resurfaced
(e.g., the
metal dome of the Indian-style digester).
*
Occasional (at irregular or infrequent
intervals) Activities:
Check the
digester, particularly Chinese-style
digesters,
for any gas leaks. Also, examine
components in
high-technology units such as pumps and mixers, which
require
occasional repair or replacement.
Finally, preventing sand, dirt, and gravel from mixing with
dung
as it is being collected, and protecting the dome of the
digester
with a metal or asphalt coating, will lengthen time between
maintenance.
IV. COMPARING THE ALTERNATIVES
CURRENT RESEARCH AND DEVELOPMENT
Biogas Generation Technology
Extensive research continues with the various biogas
generation
plants operating worldwide.
Various institutions throughout the
world are conducting research toward making maximum use of
the
biogas produced.
This involves matching energy needs to gas
production, and using equipment that burns or converts the
gas
more efficiently.
Additional research deals with digester designs
and design parameters; here, heat losses and maintaining an
adequate, stable temperature in the digester are of prime
interest
to researchers in their efforts to maximize methane
production.
Other research efforts focus on improvements in the use of
digester effluent to promote maximum growth of algae, fish,
aquatic vegetation, and farm animals.
Competing Technologies
More sophisticated and expensive biomass conversion
technologies
exist to convert organic material to charcoal, producer gas,
crude oil, simple sugars, alcohol, plastics, or other
chemicals.
Pyrolysis, which may be used to produce crude oil, for
example,
or distillation, which yields ethyl alcohol, are examples of
these technologies.
These technologies have been introduced in
many developing countries, but further research is required
before
they can be widely applied.
COMPARISON OF TECHNOLOGIES
This paper focuses on biogasification as a means of
producing
fuel from material that might otherwise be wasted or that
has
only a single end use, for example, as fertilizer.
The alternative
biomass conversion technologies are burning raw waste to get
rid of it, composting, distillation, burning raw waste to
provide
process or other beat, gasification, and pyrolysis.
To compare
all of these technologies, you must examine each technology
separately, weighing its advantages and disadvantages and
taking
into account such factors as the availability and cost of
capital,
energy costs, the relative value of a particular raw waste
and the end products it produces, the availability of human
and
material resources, and the impact of the technology on the
environment. The
discussion below presents some examples of the
kinds of factors you need to consider in balancing one
technology
against another.
If the sole objective is to reduce waste, burning raw waste
may
be a good choice, provided it is sufficiently dry, air
pollution
is controlled, and there is a means to dispose of the
ash. One
disadvantage of burning raw waste for disposal is that it is
a
very inefficient use of energy.
The energy produced by burning is
wasted. In some
situations, simply making the waste material
available to people who can use it for cooking fuel may be a
more
effective means of disposal.
And it does help assure that the
heat energy will be put to use.
Composting is an excellent way to turn waste products into a
commodity--fertilizer--simply and economically.
One disadvantage
of composting is that some of the nutrients in the raw
waste--
particularly nitrogen, phosphorus, and potassium--convert to
a
gas, evaporate, and are lost to the atmosphere, or they
leach out
through the soil.
Moreover, composting is limited to producing
only fertilizer.
If you want to do more with raw waste than composting or
just
getting rid of it--that is, if you want to harness the
energy
from the raw waste material to produce fuels or other
products--
you will need to make additional investments in capital,
materials,
and labor. As we
have seen in this paper, a biogas digester
yields both a fuel gas and a high quality fertilizer.
Unlike
composting, the digestion process retains and even improves
the
nutrient value of the original feedstock.
With biogasification,
raw wastes can be digested, and returned to the environment
in
the form of fertilizer and fuel, without degrading the
environment.
Keep in mind, however, that the equipment (e.g., a digester,
systems, pumps) necessary for biogasification will generally
be more expensive than the equipment (e.g., a wagon equipped
with
a loader, a manure spreader) necessary for composting.
The remaining four biomass conversion
technologies--distillation,
controlled burning to provide process or other heat,
gasification,
and pyrolysis--collectively produce an even wider range of
products than biogasification.
Distillation of raw wastes produces
sugar and alcohol, for example; controlled burning produces
heat to, say, a boiler.
Pyrolysis produces biofuels such as
charcoal and crude oil; and gasification produces still
other
biofuels such as low- and medium-energy gas (often called
producer
gas). These four
technologies differ chiefly in their
equipment requirements (i.e., depending on the technology,
the
hardware can be as simple as a cookstove or retort or as
intricate
as a distillation plant), in their techniques (i.e., some
techniques are more complex than others, resulting in higher
product yields), and in costs.
In sum, comparing one biomass conversion technology with
another
must be based on what end products you want from the
technology,
end product user how much you are willing to spend, relative
economies of scale, skill levels, availability of raw waste
materials, environmental impact, and many other factors.
V. CHOOSING THE TECHNOLOGY RIGHT FOR YOU
ECONOMIC IMPACT
Economics are a major factor in deciding whether or not to
introduce
a biogas system. To
determine the economics of such a system,
you need to consider such factors as availability and cost
of biogas (based on BTU), cost of equipment, capital costs,
labor
costs, energy availability/needs/cycles, material
availability
and costs, and anticipated returns.
Remember, also, to factor
into the cost analysis inflation and capitalization
expenses. All
cost factors and the resulting analysis will vary from
country to
country.
SOCIAL/CULTURAL IMPACT
Certain social/cultural questions need to be addressed.
For example,
is daily waste handling acceptable or taboo? Moreover, to
succeed, a biogas technology must interface with existing
practices:
can existing waste management practices be adapted, for
example, to include a digester and effluent disposal? What
happens
to the very poor who have traditionally collected cattle
dung freely to use for fuel when the dung is used in a
digester
and the fuel is available only to those who can pay for it?
Who
controls the distribution of the gas in a community system?
AVAILABILITY OF RESOURCES
Technical resource considerations include taking into
account the
availability of a constant, high-quality supply of organic
material,
the suitability of the ambient temperature, the availability
of good-quality water with which to dilute the feedstock,
whether the biogas produced can be used efficiently, and
whether
the space is sufficient for effluent disposal and
usage. Moreover,
keep in mind the need for a biogas plant, whose construction
and operation depend upon the availability of capital,
personnel (skilled and semiskilled), and materials.
REGULATIONS
Consult local officials about any local regulations and laws
that
may prevent you from building or using a biogas
generator. On the
positive side, some laws might work in your favor.
For example,
the governments of some developing countries provide
investment
incentives, grants, or low-interest loans to people who want
to
introduce a biogas plant.
Such governments are actively pursuing
national policies that would reduce dependence on imported
fuels
and so encourage the production of biogas as an
environmentally
safe fuel source.
LOCAL MANUFACTURE
Chinese- and Indian-style biogas generators can generally be
built in-country, since plant components are usually
available
locally. Certain
components, i.e., the dome and guide mechanism
of an Indian digester, can be manufactured on a larger scale
and
sold to users.
SCALE OF PRODUCTION AND POTENTIAL MARKET
Subsistence farmers who depend on firewood for cooking and
heating
comprise a substantial percentage of the world's population.
Though biogas generation seems likely to at least supplement
their current energy supplies, there are several reasons why
biogas may not totally replace firewood:
*
raw waste from the equivalent of several
cows is required
to meet a
family's cooking needs;
*
nearly all of the biomass conversion
technologies require
investments
of capital usually available only to a few
people in
society;
*
cultural norms may not permit waste handling
or gas
usage, or may
limit availability of organic material if
animals are
pastured rather than confined; and
*
biogas generation must be accepted and
learned, a process
dependent on
motivated, knowledgeable extension agents
or others who
can point to successful applications of the
technology,
or who can demonstrate it effectively.
SOURCES OF INFORMATION ON BIOGAS
PLANTS
Director, Gobar Gas Scheme
Khadi and Village Industries Commission
Gramodaya
Irla Road, Vile Parle (West)
Bombay 400 056 INDIA
Head of the Division of Soils Science and Agricultural
Chemistry
Indian Agricultural Research Institute
New Delhi 110 012 INDIA
Farm Information Unit
Directorate of Extension
Ministry of Agriculture and Irrigation
New Delhi, INDIA
Gobar Gas Research Station
Ajitmal, Etawah
Uttar Pradesh, INDIA
Director, National Environmental Engineering Research
Institute
World Health Organization
1211 Geneva 27, SWITZERLAND
Economic and Social Commission for Asia and the Pacific
(ESCAP)
Division of Industry, Housing, and Technology
United Nations Building
Bangkok 2, THAILAND
Bangladesh Academy for Rural Development
Comilla, BANGLADESH
Appropriate Technology Development Organization
Planning Commission
Government of Pakistan
Islamabad, PAKISTAN
CEMAT
Apartado 1160
Guatemala, GUATEMALA
OLADE
Casilla 119
Quito, ECUADOR
Volunteers in Technical Assistance (VITA)
1815 North Lynn St., Suite 200
Arlington, VA 22209 USA
BIBLIOGRAPHY
Barnett, A.; Pyle, L.; and Subramanian, S.K. Biogas
Technology in
the Third World:
A Multidisciplinary Review. IDRC-103e.
Ottawa, Ontario,
Canada: International Development Research
Center, 1978.
Brace Research Institute. MacDonald College of McGill
University.
A Handbook on
Appropriate Technology. Ottawa, Ontario, Canada:
Canadian Hunger
Foundation, 1976.
Hills, D.J., and Roberts, D.W. "Basic Fundamentals of
Methane
Generation from
Agricultural Waste." Extension service
paper,
University of California, Davis, 1980.
House, D. The Compleat Biogas Handbook. Aurora, Oregon,
1980.
McGarry, M.G., and Stainforth, J. Compost, Fertilizer, and
Biogas
Production from
Human and Farm Wastes in the People's Republic
of China.
IDRC8e. Ottawa, Ontario, Canada: International
Development
Research Center, 1978.
Lichtman, R.J. Biogas Systems in India. Arlington, Virginia:
VITA, 1982.
Pohland, F.G., ed. Anaerobic Biological Treatment Processes.
Advances in
Chemistry Series 105. Washington, D.C.: American
Chemical
Society, 1971.
Shuler, M.L., ed. Utilization and Recycled Agricultural
Wastes
and Residues.
Boca Raton, Florida: CRC Press, Inc., 1978.
Subramanian, S.K. Bio-gas Systems in Asia. New Delhi, India:
Management
Development Institute, 1977.
Targanides, P. "Anaerobic Digestion of Poultry
Waste." World
Poultry Science Journal 19 (1962):252-61.
Tatom, J.W. "Pyrolysis Experience in the Developing
Countries."
Proceedings,
Big-Energy '80 World Congress and Exposition.
Washington,
D.C.: Bio-Energy Council, 198, pp. 180-85.
SUPPLIERS AND MANUFACTURERS
OF BIOGAS PLANT EQUIPMENT AND ACCESSORIES
Patel Gas Crafters Private Limited
1/2, Shree Sai Bazar Centre
Bombay 54, INDIA
Santosh Engineers
11 Swami Vivekananand
Nagar Varanasi 221 002 INDIA
========================================
========================================